
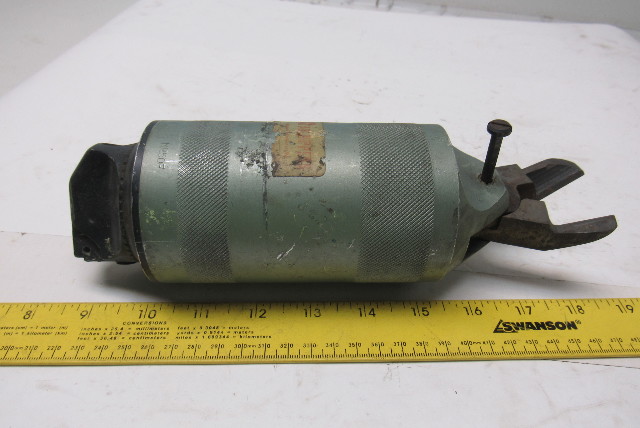
The cutting inserts with magnetic resetting are nearly maintenance-free of springs superfluous and significantly increases the safety of the robot gripper. For over two years ASS offers selected nipper blades with magnetic resetting, they can replace one-on-one the ones with spring return. If necessary, also customized special nipper blades may be manufactured and used.īy default the cutting inserts come with a spring return. To cover the different tasks of application in plastic injection moulding optimally the nipper blades have steel alloy or carbide insert and various cutting lengths of ten to 50 millimeters. The nipper blades are available in a variety of geometries: straight versions SEG (nipper blade straight), SEK inserts for pinching, as well as various SES standard inserts with angular positions of 15° to 40°, 90° angled inserts SEW and Z-shaped nipper blades SEZ. The achievable actual cutting force is always dependent on the used nipper blades and the air pressure. For light cutting tasks there is a model with 150N available. The strongest nipper has a maximum of power: cutting force of 7,700 N at 0.6 MPa. The nippers are in different versions available: automatically or manually operating, single or double acting, force amplified, round, square or regular. The original ASS Robot Hand Kit (EOAT) offers more than 30 sprue nippers and approximately 70 different cutting inserts, so called nipper blades for almost unlimited applications. Nippers and nipper blades for various cutting tasks To meet these standards, the parties always develop new de-gating solutions. In particular in the automotive plastic injection moulding have high quality standards. Much of these cutting tasts is done by sprue-nippers:ĪSS Maschinenbau offers to a wide range of nipper bodies and nipper blades in order to solve the different tasks. For example, sharp knives, heated wires or blades, laser technology or mechanical solutions such as a separating drum.
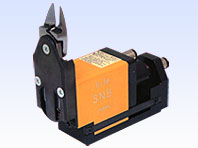
For de-gate various options are available. In further production process the sprues are usually removed. Most plastic products from the injection moulding machine have sprues, (electroplating) tabs, overflows or ridges. In the plastics industry, one of the first steps after the plastic part is extracted from the injection moulding machine is the separation of sprues.
